Driving Innovation
Rubiscape's Impact in the
Quality Team
Solutions build with Rubiscape
Implement Rubiscape’s AI-enabled Solutions! Geared for the future!
No Downtime: Predict Perfect Maintenance
AI foresees future breakdowns, preventing downtime and optimizing equipment lifespan.
Goal
- To predict the status of the water pump at any given time.
- To forecast the status of the machine beforehand.
- To predict the status of the water pump at any given time.
- To forecast the status of the machine beforehand.
Technique
- Statistical Analysis, SMOTE, Predictive Maintenance Analysis, Time Series Forecasting, Long short-term memory networks (LSTM), Visualization.
- Statistical Analysis, SMOTE, Predictive Maintenance Analysis, Time Series Forecasting, Long short-term memory networks (LSTM), Visualization.
Impact
- Breakdown of water pumps are very expensive and could be fatal ​.
- Pumps can be stooped in advance to avoid breakdown. ​
- Breakdown of water pumps are very expensive and could be fatal ​.
- Pumps can be stooped in advance to avoid breakdown. ​
Flawless Vision: AI Secures Optical Quality
Precision meets speed with AI-powered inspection, ensuring superior optics in every product.
Goal
- To ensure manufacturing precision and reliability.
- To quickly identify cracks, porosities, or surface imperfections on the cylinder head using computer vision.
- To separate defective cylinder heads from those meeting quality standards based on computer vision results.
- To ensure manufacturing precision and reliability.
- To quickly identify cracks, porosities, or surface imperfections on the cylinder head using computer vision.
- To separate defective cylinder heads from those meeting quality standards based on computer vision results.
Technique
- Image augmentation, Image classification, Object detection, Computer vision, Deep learning, Surface Defect Analysis.
- Image augmentation, Image classification, Object detection, Computer vision, Deep learning, Surface Defect Analysis.
Impact
- Early defect identification and process optimization contribute to lower production costs.
- Predictive maintenance based on data science models minimizes downtime and prevents unexpected failures.
- Automation reduces manual effort, leading to quicker inspections and improved production efficiency.
- Early defect identification and process optimization contribute to lower production costs.
- Predictive maintenance based on data science models minimizes downtime and prevents unexpected failures.
- Automation reduces manual effort, leading to quicker inspections and improved production efficiency.
Delight Purchase: Mastering Sales & Service
Exceed expectations, build loyalty, and fuel repeat business with exceptional after-sales support.
Goal
- To represent the root cause of failures.
- To determine the time for first failure of an equipment part and forecast number of future breakdown calls for that part.
- To identify interdependency of part failures.
- To represent the root cause of failures.
- To determine the time for first failure of an equipment part and forecast number of future breakdown calls for that part.
- To identify interdependency of part failures.
Technique
- Statistical Analysis, Root cause Analysis, Reliability Analysis, Time Series Forecasting, Visualization.
- Statistical Analysis, Root cause Analysis, Reliability Analysis, Time Series Forecasting, Visualization.
Impact
- Based on root causes of failure, location/manufacturer wise strategies can be planned to avoid early failure.
- Reduction in number of breakdown calls and associated cost.
- Early warning breakdown calls helps in taking preemptive measures.
- Identified sequence of patterns for failure of parts, helps in preventive actions.
- Based on root causes of failure, location/manufacturer wise strategies can be planned to avoid early failure.
- Reduction in number of breakdown calls and associated cost.
- Early warning breakdown calls helps in taking preemptive measures.
- Identified sequence of patterns for failure of parts, helps in preventive actions.
Flawless Vision: AI Secures Optical Quality
Precision meets speed with AI-powered inspection, ensuring superior optics in every product.
Goal
- To ensure manufacturing precision and reliability.
- To quickly identify cracks, porosities, or surface imperfections on the cylinder head using computer vision.
- To separate defective cylinder heads from those meeting quality standards based on computer vision results.
- To ensure manufacturing precision and reliability.
- To quickly identify cracks, porosities, or surface imperfections on the cylinder head using computer vision.
- To separate defective cylinder heads from those meeting quality standards based on computer vision results.
Technique
- Image augmentation, Image classification, Object detection, Computer vision, Deep learning, Surface Defect Analysis.
- Image augmentation, Image classification, Object detection, Computer vision, Deep learning, Surface Defect Analysis.
Impact
- Early defect identification and process optimization contribute to lower production costs.
- Predictive maintenance based on data science models minimizes downtime and prevents unexpected failures.
- Automation reduces manual effort, leading to quicker inspections and improved production efficiency.
- Early defect identification and process optimization contribute to lower production costs.
- Predictive maintenance based on data science models minimizes downtime and prevents unexpected failures.
- Automation reduces manual effort, leading to quicker inspections and improved production efficiency.
Do even more with Rubiscape
AI-driven organisations around the world use Rubiscape to solve their most pressing business problems.
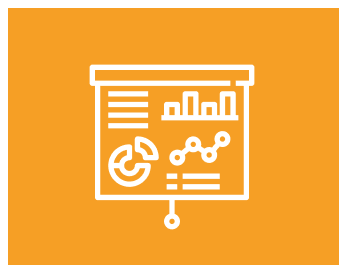
Drag, Drop, Discover:
Insights Made Simple.
Dive deep into your data, create stunning visuals, and gain actionable insights with ease.
Learn More
Learn More
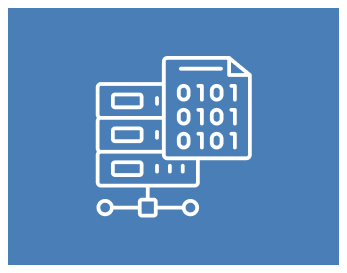
Build, Deploy, Manage:
Streamline AI Workflow.
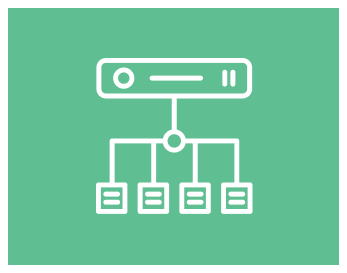
Wrangle, Blend, Analyze:
Data Orchestration Refined.
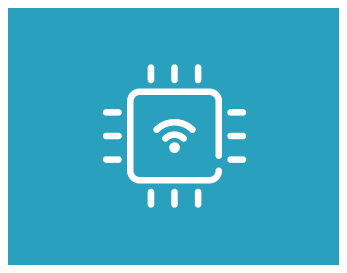